Table Of Content
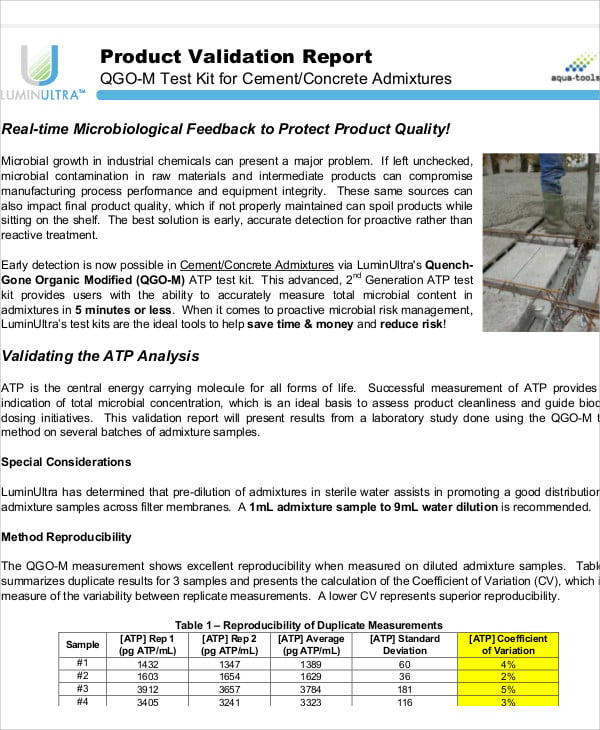
Until you see users interacting with a developed concept, prototype, or product, even they don’t know exactly how they’ll behave. Taking the time to conduct thorough user testing will save your time and money—as well as sanity—in the long run. Testing is the best way to see how your ideas, prototypes, and products perform in real environments with real users. You’ve worked tirelessly to create an amazing product and added many features you think users will love. You’re almost ready to launch, but then you discover that you’ve focused on all the wrong things. Customers don’t find the product user-friendly and it turns out they’d prefer a simple, streamlined experience over the complex feature-packed hierarchies you’ve designed.
The differences between design validation and verification
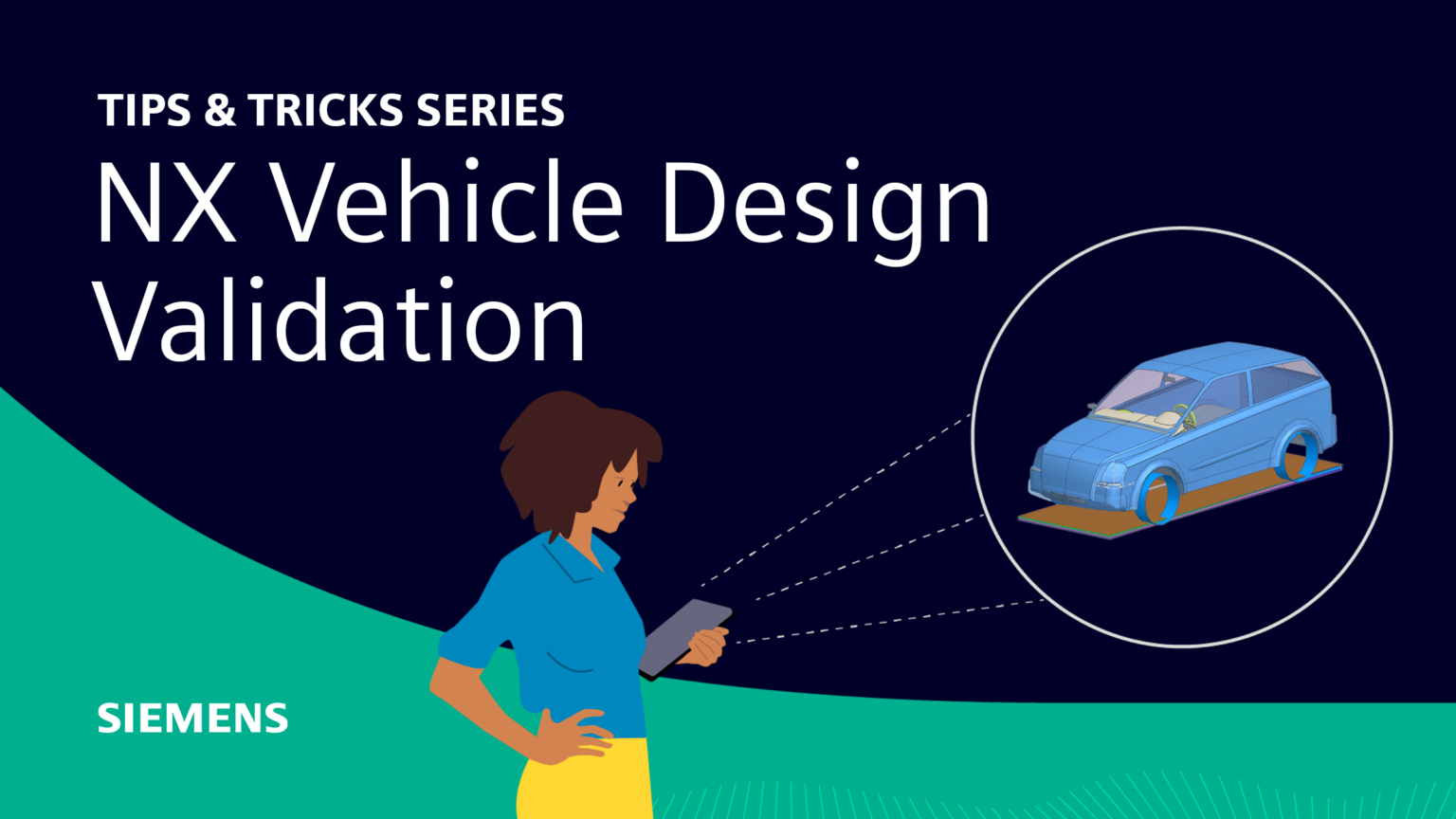
Any invalid results are documented and reviewed, and either accepted or logged as defects. Defects in the product are resolved and released, and regression testing is performed. A traceability matrix is created to verify that design inputs identified in the verification test plan have been tested and passed. Since stakeholders are key decision makers in the product design process, you can eliminate the back and forth in redoing designs by involving them from the start. As such, an effective product design needs to have essential product metrics defined. You can then measure these metrics about the product design to determine if your design is good.
Keep all your design control activities in one centralized location with Greenlight Guru
The design validation test (DVT) stage is where a product truly starts becoming industrialized. Where EVT is all about architecture-level design for manufacturing, DVT is about getting the details right while moving towards the first mass production line. PCBs are iterated to perfection through debugging and denoising efforts. The CM will develop the first hard tool for every made part to verify mass production yields. Aluminum molds may be used to optimize the design in terms of surface finish, materials, tolerancing, mold configuration such as sliders and cams, joining methods, as well as process parameters. If products are not verified to be implemented according to the design specifications, then there could be potential inconsistencies in user experience.
Advantages of design validation and verification
We all put so much work into our designs and sometimes being objective is really hard! Do not let preconceived notions get into your head when engaging in the validation of your design. UXers at Google revamped Google’s material design after conducting a very comprehensive design validation consisting of heuristic evaluations, usability tests, and peer reviews! Start by pinpointing the specific design or feature that you would like to validate.
Improved antitumor activity through a tyramidyl maslinic acid derivative. Design and validation as drug-loaded ... - ScienceDirect.com
Improved antitumor activity through a tyramidyl maslinic acid derivative. Design and validation as drug-loaded ....
Posted: Wed, 15 Nov 2023 20:07:01 GMT [source]
Also, ensure there is maximum and efficient teamwork among the designers, engineers, quality control team, and testing team. This will ensure that your validation process is comprehensive and touches on every aspect of the product. It’s worth noting that a product design may meet the verification requirements but fail to satisfy validation. This can happen especially if there were flaws in the product requirements or specifications.
This comprehensive approach to design verification helps identify and rectify any potential issues or shortcomings early on, leading to a more robust and reliable end product. Medical device design verification is the process of testing to specification. It’s a technical process that verifies that your product does everything you claim it can do. For all devices and design controls, you should have clear, measurable specifications, called design inputs. Then, you take representative units of your final device, test them, and compare those results to ensure they meet the predetermined acceptance criteria.
When was the last time the No. 1 overall NFL draft pick came from USC?
A/B testing revolves around testing designs with a single variation to determine which performs better. This is a great method to use if your design validation objective is linked to a specific metric such as goal completion or a conversion rate. The final step is to iterate your initial design and act on your potential solutions. Please keep in mind that UX validation is an iterative process so make sure to monitor the performance of any design modification to ensure a positive contribution to your KPIs. Planning for complex testing needs might seem daunting but it is a must if you want to get actionable results within a satisfactory period! Make sure to factor in extra time for participant recruitment as well as plan extra time for analysis.
Crafting Confidence: A Comprehensive Guide to Design Validation Plans
The first returns will come in, and EFFA analysis will ensure that all failed units make it back to the engineering team. To further guarantee the quality, factories and vendors need to be supervised to make no unforeseen changes in tooling or process parameters leading to quality shifts. The overall focus is on yield improvement, cost reduction, and expansion where necessary. The marketing and sales team here can focus on developing collateral, advertising, as well as predicting sales volumes.
Use Tools With End-to-End Traceability
If you spot deviations or issues, decide whether they’re tolerable or need design modifications. This whole process may require revisiting the design validation process repeatedly. The product development process should be flexible enough to allow room for future upgrades or changes. The best way to ensure this is possible is by documenting your validation plan.
He has both manufacturing and product development experience, even aiding in the development of combination drug-delivery devices, from startup to Fortune 500 companies and holds a Project... In this episode of the Global Medical Device podcast, we delve into everything related to design verification and validation, which is often called V&V. Probably the most misunderstood concept in the design requirements of ISO 9001, if not the entire standard, is the difference between Design Verification and Design Validation. These two steps are distinctly different, and important in a good design process.
Each stage contains room for learning, exploration, and adaptation, while a product has to pass defined criteria before moving forward to ensure successful industrialization. They’re steps in your design controls that are intimately connected to the rest of product development. And making sure those connections are clear and fully traceable is a fundamental requirement for any medical device company’s QMS.
By adhering to the FDA’s requirements for design verification and validation, medical device manufacturers can ensure the development of safe, effective, and compliant devices. These activities play a crucial role in mitigating risks, identifying design flaws or deficiencies, and ultimately delivering high-quality products that meet the needs of healthcare professionals and patients. In terms of design validation, the FDA emphasizes the importance of conducting validation activities throughout the entire design process. Manufacturers are required to establish and follow a validation protocol that outlines the approach, methods, acceptance criteria, and responsibilities for each validation activity.
Using a tool with strong requirements-to-test-to-results trace capability will help you identify holes in coverage and give early warnings on fragile or untested areas in the product. Verification of the product requirements, as above, shows that the product does what we said it would do. We’ve identified our user needs; now let’s identify what the device has to do and how it has to do it. It’s crucial to carry out comprehensive documentation as it will be useful in compliance, auditing and referencing in the future. Every validation result, decision, and modification performed should be documented. The documentation forms a part of the history of the project and is useful for continuous improvement.
Testing is the final stage in the design thinking methodology, which is a five-stage product design process that helps teams develop creative solutions. As with design inputs, be sure that your user needs are clearly defined at the beginning of the design and development process. For example, if one of the user needs is that “the device needs to be safe,” how will you validate that?
No comments:
Post a Comment